
Contact : Claire
Courriel : sales3@mooreplc.com
Tél/whatsapp:+86-18150117685
Les robots collaboratifs sont bon marché et faciles à programmer et à déboguer. Ils apparaissent de plus en plus dans la fabrication, l'emballage, la fabrication d'aliments et de boissons, et font jaillir l'industrie.
Récemment, un fournisseur de composants automobiles a utilisé des robots collaboratifs pour innover en matière de fabrication. L'entreprise est Comprehensive Logistics, qui fabrique des suspensions, des groupes motopropulseurs et des composants intérieurs pour deux des plus grandes entreprises automobiles d'Amérique du Nord. L'usine avait besoin d'un moyen reproductible pour inspecter la chaîne de sous-assemblage du support moteur et a trouvé une solution sur le robot Unirox.
L'inspection automatisée du sous-ensemble de support de moteur est un défi, y compris un connecteur de faisceau de faisceau de direction critique qui doit également être synchronisé avec la haute capacité de la ligne tout en garantissant une connexion correcte aux connecteurs électriques du faisceau.
Initialement, les constructeurs automobiles utilisaient un système multi-caméras fixe, mais ne pouvaient pas positionner la caméra dans une position compacte. Les données recueillies par le système de caméras fixes n'étaient pas aussi complètes. L'entreprise a également essayé des robots sondes et des programmes de détection manuelle. Le programme n'a pas amélioré la répétabilité.
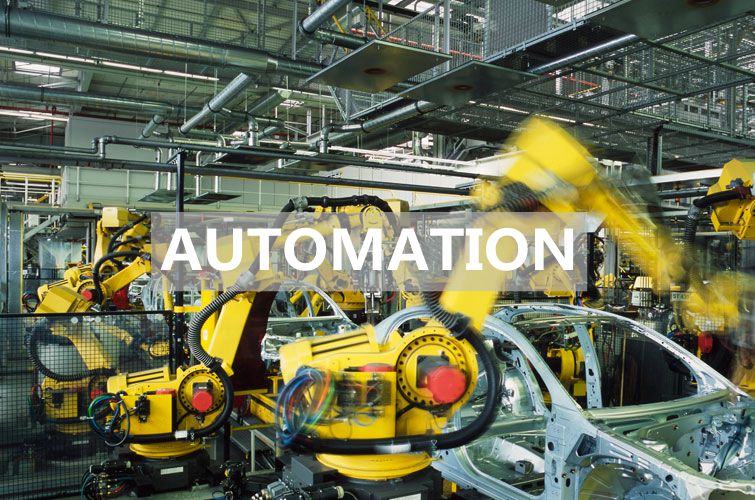

La nouvelle solution utilise le plus grand robot collaboratif UR10 et la caméra CV-X de Keyence, qui fait partie du système de vision CA-HX200C LumiTrax pour naviguer dans les unités de sous-ensemble et fournir des résultats de test reproductibles. Le robot coopérant UR10 monté au plafond se déplace rapidement entre les points de contrôle, permettant à la caméra CV-X de capturer chaque image connectée avant que le bras de coordination ne se rétracte dans sa position d'origine, puis d'attendre que le prochain composant soit inspecté.
Lors de l'inspection du sous-ensemble, chaque image est immédiatement affichée sur l'écran à côté du robot, tandis que le deuxième écran avec la carte du support moteur montre que chaque point de contrôle est complété par une coche verte ou rouge pour indiquer la réussite/l'échec. Le Manufacturing Execution System (MES) de l'entreprise collecte les données de réussite/échec et stocke ces informations sur la carte mémoire de la caméra pendant deux jours.
Les supports de moteur diesel et à gaz ont respectivement 11 et 9 points de contrôle, et tout produit de moteur doit être identifié. L'identification des différents types de moteurs et d'autres données critiques nécessite que le système de robot et de caméra communique avec le contrôleur logique programmable (PLC) de la chaîne de montage via Industrial Ethernet.
Le système exécutera le premier passage à tous les points de contrôle, et si un paramètre échoue, le système se réinitialisera. Chaque station a un temps takt de 60 secondes sur la chaîne de montage, le temps de cycle d'inspection est d'environ 48 secondes et le cobot UR10 prend environ 32 secondes. Ce paramètre permet au temps de réexécution d'échouer et l'ensemble de la chaîne de montage ne s'arrête pas.
Le temps d'inspection global est critique car la logistique intégrée reçoit des commandes instantanées (JIT) du constructeur automobile. Au cours des trois dernières années, les fabricants sous contrat ont reçu plus de 600 000 commandes de produits de moteur liés aux sous-ensembles.
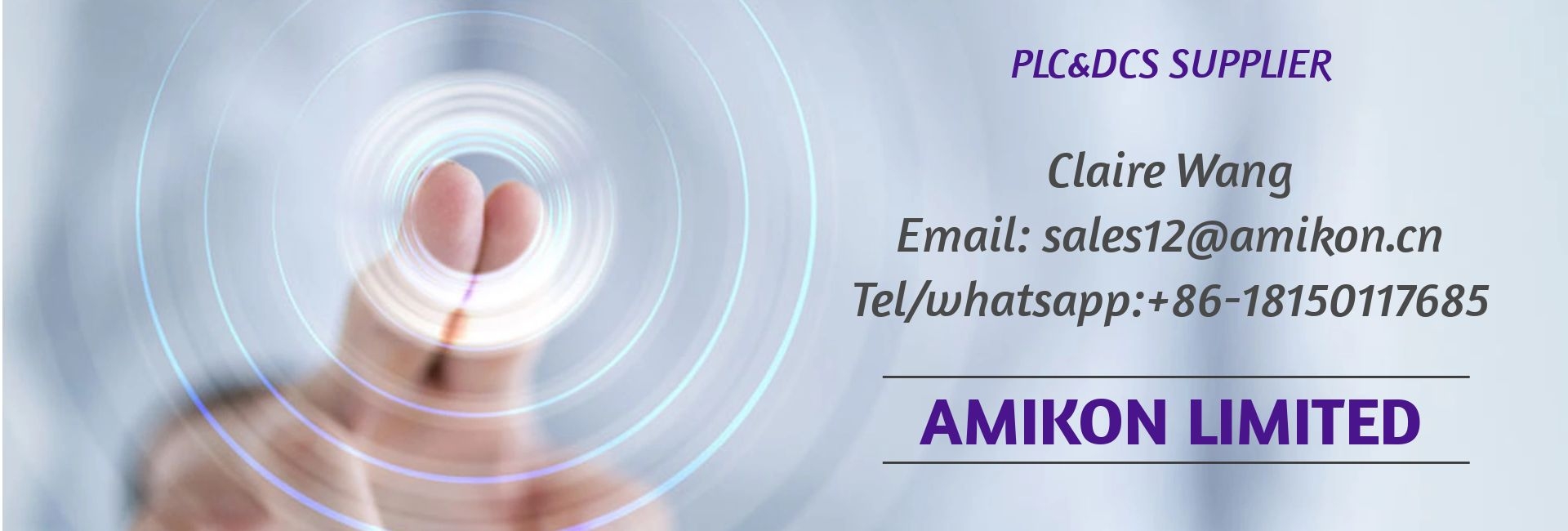